Welding is a common process for joining metal parts, but during the welding process, the occurrence of cracks may pose a threat to the performance and integrity of the welded joint. Therefore, it is crucial to take a series of measures to prevent the occurrence of welding cracks. This article will describe some key measures to reduce the risk of welding cracks.
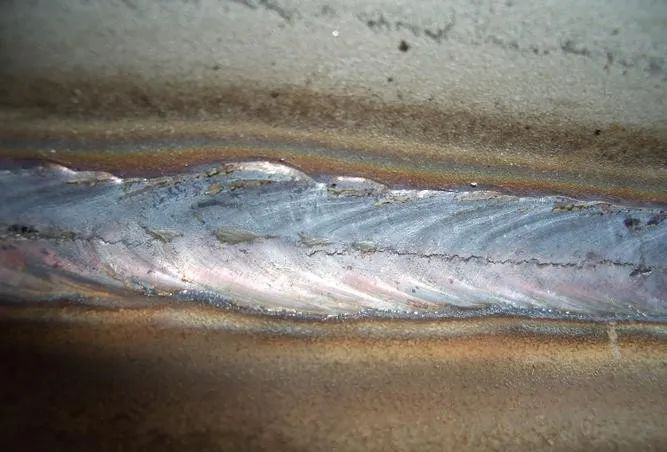
Material selection is critical to successful welding. Certain alloy materials are more prone to cracking. Therefore, during the welding process, appropriate materials should be selected taking into account their heat resistance and welding characteristics.
2. Control welding parameters
Welding parameters, such as current, voltage, welding speed and angle, etc., should be controlled according to specific conditions. Appropriate parameter settings can reduce heat-affected zones and stress accumulation, reducing the risk of cracks.
3. Choose the appropriate welding technology:
Different welding techniques are suitable for different materials and applications. For example, TIG welding is suitable for thin plate welding, while MIG welding is suitable for high-strength materials. Choosing the right welding technique is key to preventing cracks.
4. Quality control and testing:
Potential welding problems can be discovered promptly using appropriate quality control methods such as X-ray inspection, ultrasonic inspection or penetrant inspection. These methods can be used to verify weld quality and integrity.
5. Quality control and testing:
Training experienced welding operators can better predict and avoid cracks. Accumulation of experience is an important factor in preventing welding cracks.