Mechanical equipment in the transportation industry, such as cars, trains, airplanes, ships, etc., are subjected to extreme working conditions every day, and their parts and components inevitably experience severe wear and corrosion. Replacing wearing parts has always been an expensive and time-consuming task during repair and maintenance, which not only increases costs but also results in downtime of mechanical equipment. However, in recent years, the introduction of plasma cladding technology has provided a new solution to this problem.
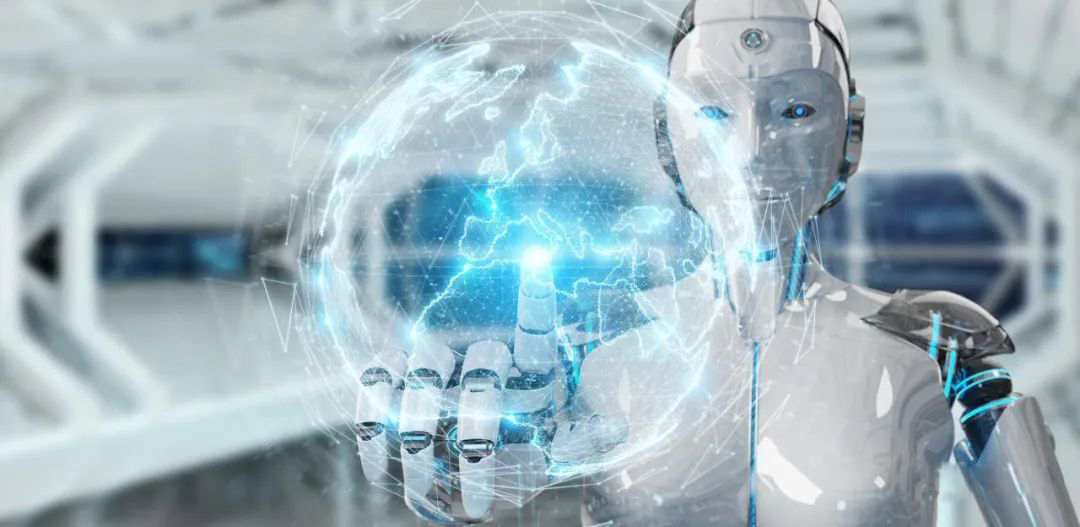
What is plasma cladding?
Plasma surfacing is a high-heat welding technology that uses the high temperature generated by the plasma arc to melt metal or alloy powder, and then spray-welds it on the surface of the part to achieve repair and reinforcement. This technology is widely used in the repair, enhancement and remanufacturing of metal parts. Its advantage is that it can accurately control the heating temperature and welding area, reducing the impact on the base material.
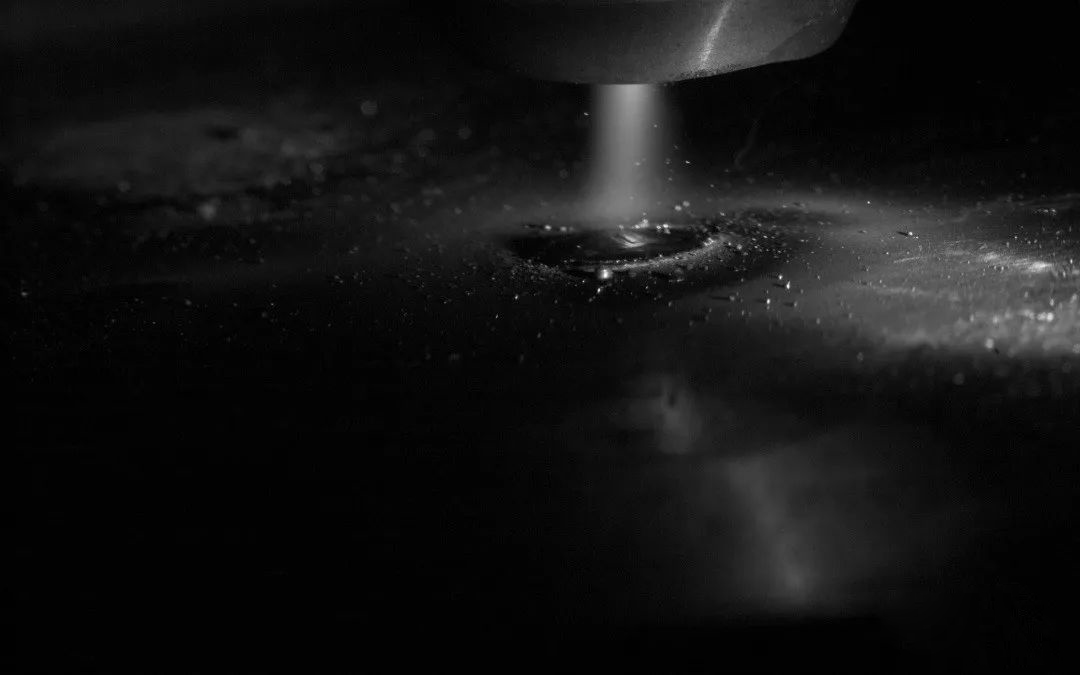
Application of plasma surfacing in transportation vulnerable parts
Engine cylinder liner repair
The engine is the core of transportation, and its performance and reliability are directly related to safety and efficiency. However, engine cylinder liners are often damaged by high temperatures and pressure, and traditional repair methods often require replacing the entire engine, which is extremely costly. Plasma cladding technology creates a strong, wear-resistant coating on engine cylinder liners, extending their service life and saving on expensive replacement costs.
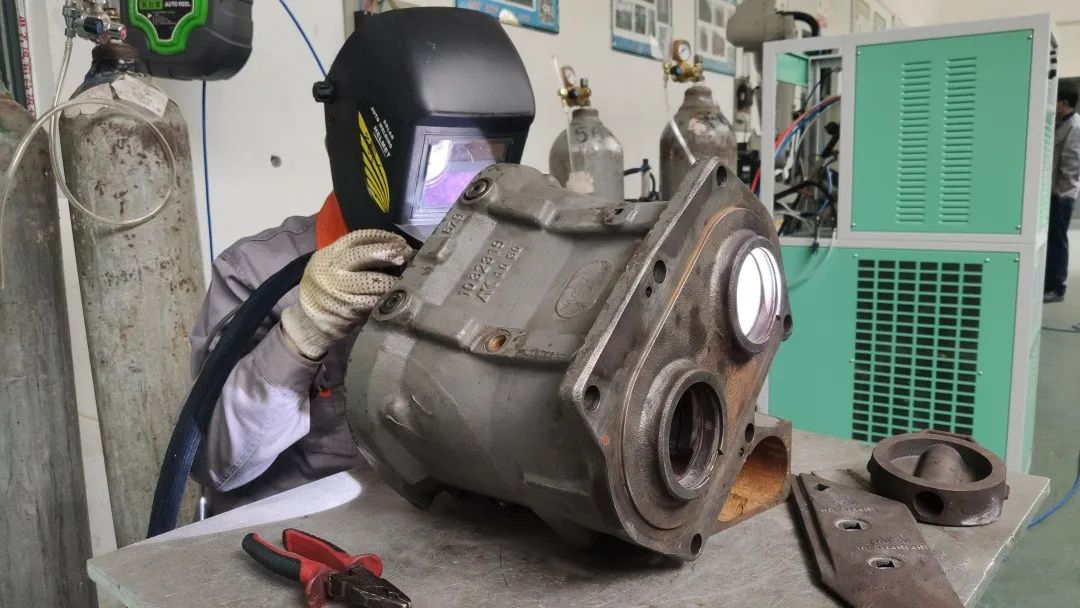
Aircraft landing gear maintenance
Aircraft landing gear is subject to huge impacts and pressures, and the repair of vulnerable parts is crucial to flight safety. Plasma surfacing technology can be used to repair damage to landing gear parts and restore their original performance. Through customized welding procedures, welding quality can be fully controlled and the integrity of parts can be guaranteed.
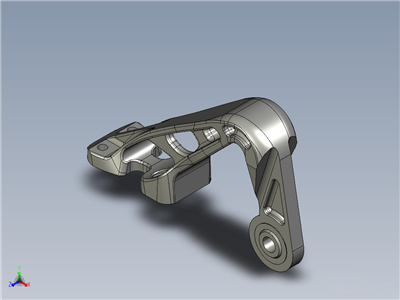
Ship propeller repair
The blades of ship propellers are often affected by seawater corrosion and collisions and require regular maintenance. Traditional repair methods may require disassembly of the entire propeller, which is time-consuming and labor-intensive. Plasma cladding technology allows for on-site repairs on ships, enhancing thruster performance and reducing maintenance time and costs by applying a high-strength, corrosion-resistant coating.
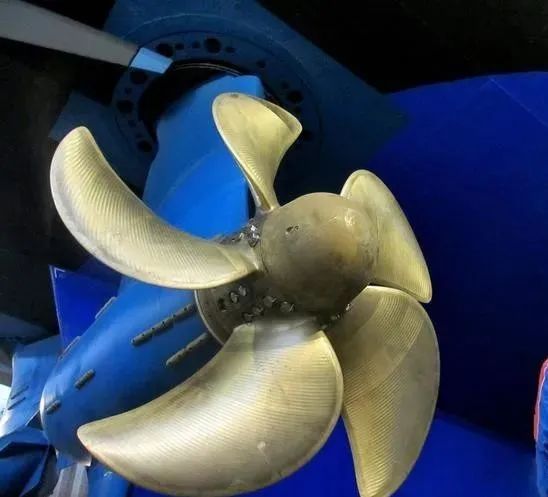
Why choose plasma cladding?
Plasma cladding can restore parts to their original performance, avoiding expensive parts replacement costs. Additionally, it reduces downtime and increases equipment availability.
Plasma surfacing technology can achieve complete control of welding temperature, welding area and coating thickness, ensuring the accuracy and quality of the repair process.
Plasma cladding produces less scrap and has a smaller environmental impact than traditional part replacement methods.
Multi-material applicabilityPlasma cladding produces less scrap and has a smaller environmental impact than traditional part replacement methods